The coating temperature of PECVD electric furnace varies depending on the process stage and material characteristics. Let’s take a detailed look below!
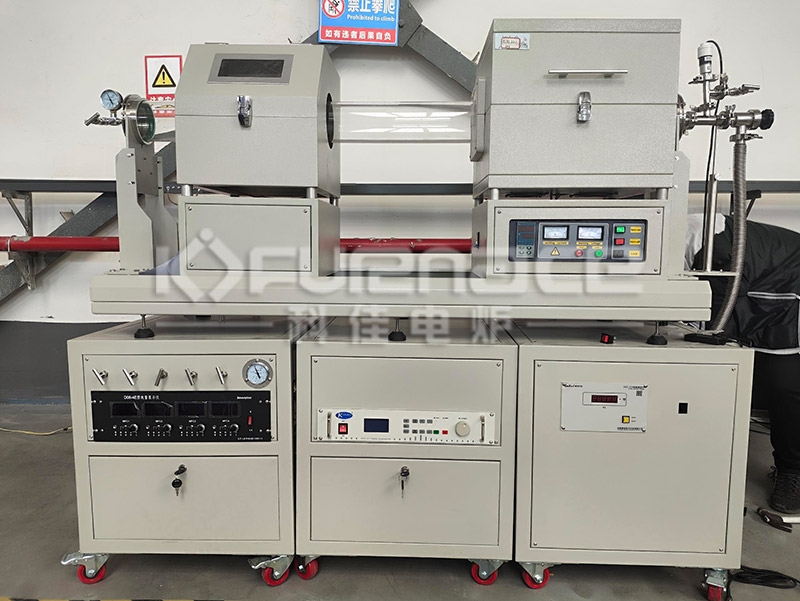
PECVD slide furnace commonly used for graphene growth (click on the image to view product details)
1. Coating temperature range
Basic coating temperature
The PECVD process allows for the adjustment of substrate temperature within the range of room temperature to 400 ℃, with common operating temperatures ranging from 200 ℃ to 450 ℃. For example, during polycrystalline silicon coating, the furnace tube temperature is often set at 450 ℃, and the annealing stage temperature can be raised to 500-850 ℃.
Temperature difference during the process stage
Ammonia blowing stage: temperature control at 400-450 ℃
Pre sedimentation stage: temperature maintained at around 440 ℃
Chemical reaction gas ionization stage: temperature stable at 430-460 ℃
Polycrystalline silicon annealing stage: The temperature range can reach 500-550 ℃
2. Temperature control accuracy requirements
High precision temperature control requirements
By adopting PID control and self-tuning adjustment technology, a temperature control accuracy of ± 1 ℃ is achieved. For example, the continuous PE-CVD coating equipment is equipped with a LCD touch control system that supports 30 programmable temperature curve settings.
Key parameter control direction
Film performance adjustment: deposition rate controlled by RF power (adjustable from 0-500W) and nitrogen flow rate
Thin film stress optimization: Using the temperature of the lower electrode to control the density of the thin film, every 100 ℃ increase in temperature can increase the density of the thin film by 15% -20%
Chamber pressure control: Under the same flow conditions, precise control of membrane stress within the range of -260MPa to+500MPa can be achieved by adjusting the chamber pressure
3. Special process temperature characteristics
Advantages of low-temperature sedimentation
Utilizing plasma energy to achieve low-temperature deposition (from room temperature to 350 ℃), avoiding damage to the substrate caused by high temperatures. For example, when depositing silicon nitride films on plastic substrates, the process temperature can be controlled below 250 ℃.
The necessity of high-temperature annealing
After coating, high-temperature annealing treatment at 600-850 ℃ is required to achieve a hydrogen atom concentration of 10 ㎡⁰ -10 ㎡² cm ⁻ ³ in the polycrystalline silicon layer, significantly improving the electrical properties of the film.
4. Precautions
Temperature uniformity: The temperature distribution inside the furnace needs to be uniform, otherwise it may cause uneven film thickness or composition.
Process compatibility: High temperature may cause interface diffusion between the substrate and the film (such as metal substrate oxidation), which needs to be evaluated in advance.
Safety control: High temperature processes require strict control of gas flow and cooling systems to avoid explosions or equipment damage.
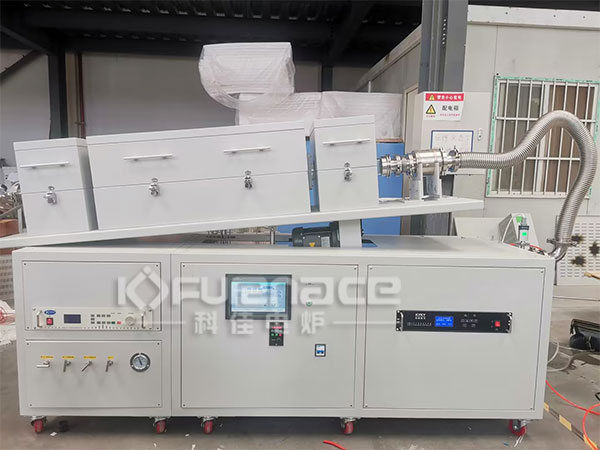
Customized tilted rotating PECVD coating electric furnace (click on the image to view product details)
When selecting, if more specific temperature parameters are needed, it is recommended to refer to the process manual of the equipment used or consult the PECVD equipment supplier, as technical parameters from different manufacturers may vary.Click to learn more PECVD devices! Or click on online customer service to learn more about product information!