Plasma enhanced chemical vapor deposition (PECVD) coating electric furnace is a device that uses low-temperature plasma assisted chemical reactions for thin film deposition. It has the advantages of low deposition temperature, high deposition rate, and adjustable thin film properties, and is widely used in semiconductor, photovoltaic, optical and other fields. Let’s take a detailed look below!
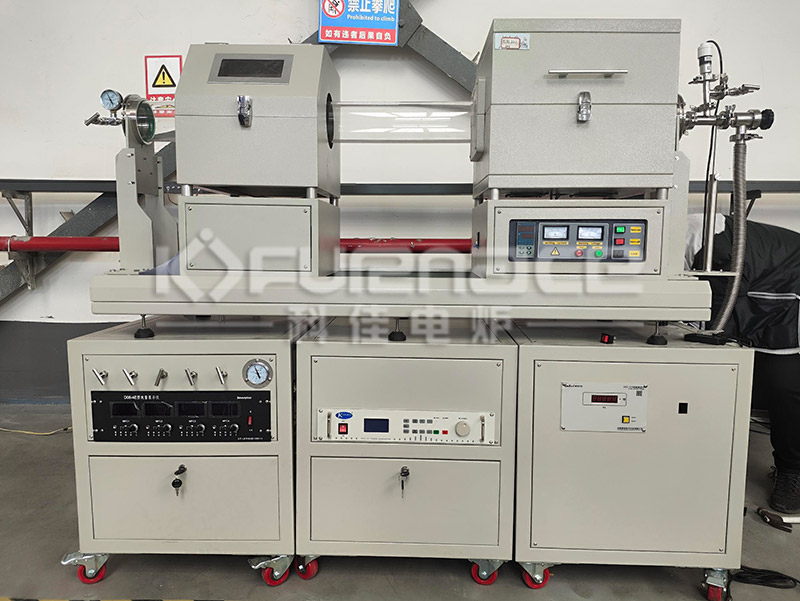
Slide PECVD tube furnace (click on the picture to view product details)
1. Core structure and working principle
Reaction chamber design
Material: Usually made of quartz material, it is resistant to high temperatures and corrosion, ensuring the stability of vacuum environment and chemical atmosphere.
Structure: divided into tube furnaces, bell jar furnaces, etc., equipped with radio frequency (RF) or microwave electrodes inside for exciting plasma. For example, a tubular PECVD furnace often adopts a horizontal or vertical tubular structure, with the substrate placed on a quartz boat or graphite tray and carried into the furnace by a carrier.
Plasma excitation method
Radio frequency (RF) excitation: A commonly used 13.56MHz RF power supply generates an alternating electric field through electrodes, ionizing reaction gases to form plasma, such as silane (SiH ₄), ammonia gas (NH3), nitrogen gas (N ₂), etc.
Microwave excitation: using low-temperature plasma to induce glow discharge at low pressure on the cathode of the deposition chamber, and using radio frequency power or microwave power to excite gas to generate plasma. Gas molecules ionize under the action of an electric field, forming charged ions and free electrons. These charged particles accelerate under the action of an external electric field, forming a plasma. The precursor gases for depositing thin films (such as silane, ammonia, etc.) undergo chemical reactions under the action of plasma, generating active species (such as free radicals, ions, etc.). These active species adsorb on the surface of the sample and undergo chemical reactions, forming a uniform and dense thin film.
2. Technical features
Low temperature deposition: PECVD allows for relatively low substrate temperatures (room temperature to 350 ° C), is friendly to high temperature sensitive materials (such as plastics), and reduces film stress and bonding issues.
High deposition rate: The presence of plasma increases the gas-phase reaction rate, enabling rapid preparation of thin films.
Adjustable film performance: By adjusting plasma parameters and deposition conditions, the crystallinity, refractive index, thickness, and other properties of the film can be controlled.
Good uniformity: The reactants in the plasma have high kinetic energy and can form high-quality thin films throughout the substrate.
Wide applicability of materials: suitable for the deposition of inorganic materials such as nitrides, oxides, carbides, silicon, and organic materials such as polymers.
Low energy consumption: Compared to other deposition techniques, PECVD can usually complete the deposition process with lower energy consumption.
3. Application Fields
In the field of photovoltaic cells, it is mainly used to prepare silicon nitride thin films, which have dual effects of passivation and anti reflection. By optimizing deposition parameters, the conversion efficiency and service life of solar cells can be improved.
Semiconductor industry: used for manufacturing integrated circuits, solar cells, etc. PECVD technology can accurately control process parameters, deposit high-quality thin films on substrate surfaces, such as silicon dioxide and silicon nitride dielectrics, for isolating multiple conductive layers and capacitors.
In the field of optics: used for manufacturing optical thin films, such as anti reflective films, reflective films, etc.
Surface engineering: used to improve the wear resistance, corrosion resistance, and other properties of material surfaces.
In the field of automotive electronics: providing waterproof, moisture-proof, and corrosion-resistant protection for battery management system (BMS) circuit boards and electronic components; Enhance the environmental adaptability of onboard sensors; Provide waterproof, anti fog, and anti scratch capabilities for car lamp lenses; Enhance the wear resistance and pollution resistance of automotive interior parts; Provide protection for motors and electronic control units; Prevent short circuits and corrosion of charging interfaces and connectors; Provide waterproof and anti fouling protection for car cameras and sensors.
In the field of medical equipment: applied to the protection of hearing aid shells and internal components, improving the waterproof and dustproof performance of equipment; Realize comprehensive protection of the surface of medical mobile phones to prevent liquid infiltration and bacterial growth; Improve the performance and service life of medical robotic arms, portable monitors, and other equipment.
4. Equipment configuration
The PECVD coating electric furnace is mainly composed of plasma source, reaction chamber, gas feeding device, vacuum pump and other parts. The plasma source generates high-energy electrons, which heat the gas through an electromagnetic field to form plasma; The reaction chamber is the main site for thin film deposition; The gas feeding device is used to precisely control the flow rate and proportion of process gases; A vacuum pump is used to evacuate the reaction chamber to a high vacuum state, ensuring the stability of the deposition process.
5. Selection suggestions
Clear requirements: Determine the required film materials, performance requirements, and production scale based on specific application scenarios.
Pay attention to technical parameters: focus on key technical indicators such as deposition temperature range, deposition rate, film uniformity, and equipment ultimate vacuum degree.
Assessing equipment stability: Select equipment suppliers with mature process experience and stable performance to ensure the long-term reliability of equipment operation.
Evaluate after-sales service: Prioritize suppliers who provide comprehensive technical support and after-sales service to facilitate equipment maintenance and process optimization.
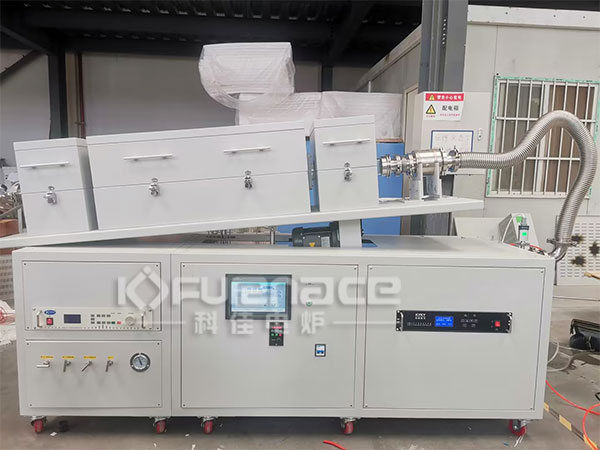
Customized tilted rotating PECVD coating electric furnace (click on the image to view product details)
6. Summary
The plasma enhanced PECVD coating electric furnace achieves high-precision thin film deposition in semiconductor, photovoltaic, optical and other fields through low-temperature plasma excitation. Its core advantages lie in low-temperature process compatibility and controllable thin film performance. When selecting equipment, special attention should be paid to temperature uniformity, vacuum degree, and plasma control accuracy to meet the requirements of different materials and processes. You can communicate the parameters with relevant technical personnel or business managers before choosing, so as to customize a plasma enhanced PECVD electric furnace that suits you!Click to learn more PECVD devices! Or click on online customer service to learn more about product information!