As a commonly used coating equipment in university laboratories, industrial and mining enterprise laboratories, chemical vapor deposition (CVD) coating experimental furnaces are widely used. So, what should be noted when choosing CVD coating furnaces? Let’s take a detailed look below!
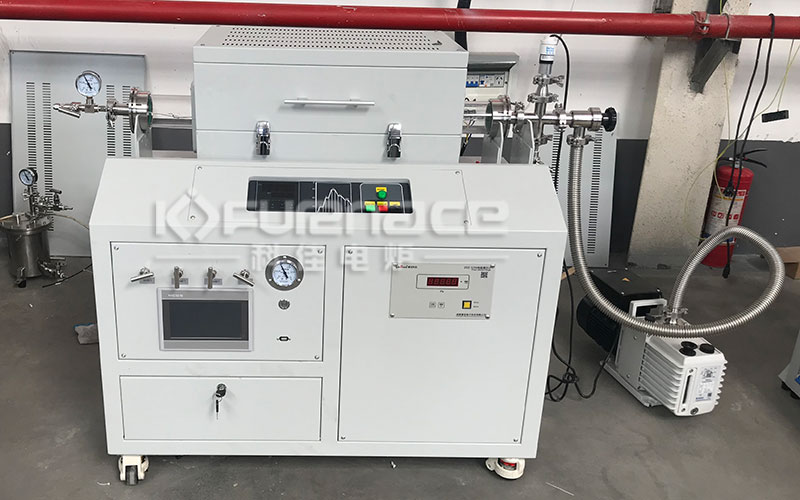
Commonly used CVD electric furnaces for silicon dioxide coating (click on the image to view product details)
1. Temperature control: Match experimental requirements to ensure accuracy and stability
Temperature range:
High temperature requirements: CVD coating experiments usually require a high temperature environment of 850-1100 ℃, and some experiments (such as metal organic chemical vapor deposition) may require higher temperatures (≥ 1200 ℃). The furnace should be selected based on the characteristics of the experimental materials, such as:
1200 ℃ Dual Temperature Zone CVD System: Suitable for experiments that require segmented heating or temperature gradients, such as integrated thin film growth and annealing processes.
1550 ℃ high-temperature CVD furnace: supports the deposition of high-temperature alloys or ceramic materials, meeting the experimental needs under extreme conditions.
Temperature accuracy and uniformity:
PID control technology: Through fuzzy PID algorithm and self-tuning adjustment, precise temperature control (within ± 1 ℃) is achieved to ensure the consistency of sintered products.
Temperature uniformity: The temperature distribution inside the furnace should be uniform (such as within ± 10 ℃) to avoid uneven heating of the sample, which may lead to a decrease in coating quality. For example, the dual temperature zone design can achieve temperature gradient through independent temperature control, meeting complex process requirements.
2. Furnace structure: optimized design to enhance stability and durability
Furnace material:
High purity alumina polycrystalline fiber: With advantages such as cleanliness and energy saving, it is suitable for CVD coating experiments, which can reduce impurity pollution and improve thermal efficiency.
Quartz furnace tube: suitable for high temperature and corrosive environments, with good transparency and easy optical monitoring (such as graphene growth).
Sealing and cooling system:
Flange sealing: Adopting clamp or water-cooled flange design to ensure the sealing of the furnace body and prevent gas leakage. For example, water-cooled flanges are equipped with lifting frames that can adjust the sealing height according to actual needs.
Double layer air-cooled structure: By using an air-cooled system, the surface temperature of the furnace body is quickly reduced, protecting the equipment and extending its service life.
3. Gas and Vacuum Systems: Precise Control to Ensure Experimental Environment
Gas supply system:
Multi channel gas design: supports the simultaneous introduction of multiple gases such as argon, hydrogen, nitrogen, alkanes, etc., to meet the requirements of different coating processes. For example, a four-way gas design can achieve precise control of gas mixing ratios.
Mass Flow Meter (MFC): Equipped with high-precision MFC (such as HORIBA brand, accuracy ± 1.0% F.S.) to ensure stable gas flow and avoid flow fluctuations affecting coating quality.
Vacuum system:
Vacuum requirement: Select the appropriate vacuum device according to the experimental requirements. For example:
Low vacuum system: The ultimate vacuum degree can reach 0.04Pa, suitable for atmospheric or low-pressure CVD experiments.
High vacuum system: The ultimate vacuum degree can reach 1.0 × 10 ⁻⁴ Pa, meeting high-end experimental requirements such as ultra-high vacuum CVD or plasma enhanced CVD (PECVD).
Vacuum pump type: Equipped with rotary vane pump or molecular pump, the pumping speed should meet the experimental requirements (such as 17m ³/h), and a filter should be installed to extend the service life of the pump.
4. Safety and ease of use: ensuring operational safety and improving experimental efficiency
Security protection measures:
Overheating protection: When the temperature exceeds the set value, it automatically shuts off and alarms to prevent equipment damage.
Power off protection: The power off function when opening the door ensures safe operation and avoids accidents during the experimental process.
Leakage protection: Install leakage protection devices to prevent equipment leakage from causing safety accidents.
Convenience of operation:
Double opening furnace door: convenient for taking and placing samples, improving experimental efficiency.
LED display screen: Simultaneously displays the set and actual temperature, facilitating real-time monitoring of the experimental process.
Cabinet design: including casters for easy equipment movement and layout adjustment.
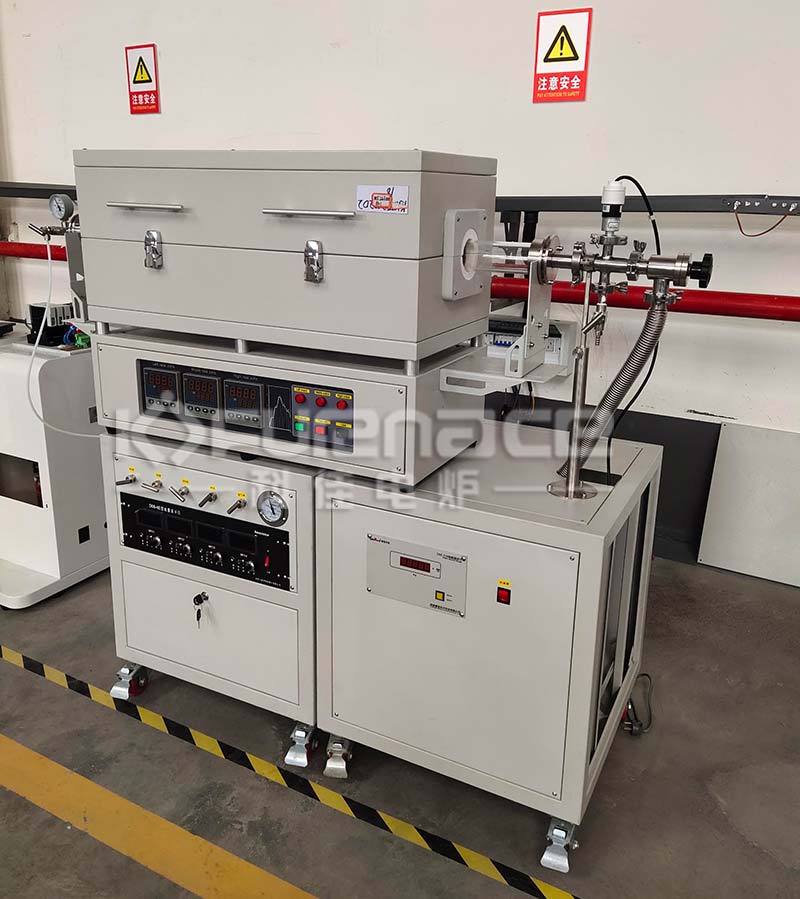
Multi temperature zone tubular CVD electric furnace (click on the image to view product details)
In general, when choosing a CVD electric furnace for chemical vapor deposition coating, attention should be paid to the above aspects. It is recommended to communicate the parameters with relevant technical personnel before selecting, so as to customize a more suitable heat treatment CVD electric furnace for oneself!Click to learn more CVD devices! Or click on online customer service to learn more about product information!