The tube furnace is designed with a multi zone structure, which can significantly improve experimental flexibility, material processing accuracy, and process applicability by independently controlling the temperature in different zones. Let’s take a detailed look below!
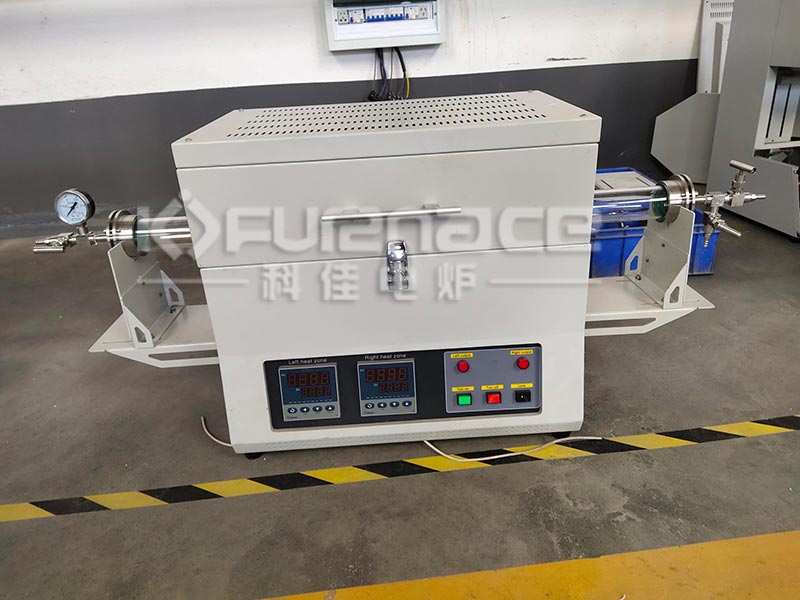
Commonly used laboratory dual temperature zone tube furnace (click on the image to view product details)
1. Realize complex temperature gradient control
Simulate the actual process environment
In material synthesis (such as CVD deposition, crystal growth) or heat treatment (such as annealing, sintering), multiple temperature zones can simulate temperature gradients in actual production. For example, in the preparation of graphene, the carbon source is decomposed in the high temperature zone (1000 ℃) in the front section, the deposition rate is controlled in the medium temperature zone (800 ℃) in the middle section, and the ordered lattice arrangement is promoted in the low temperature zone (500 ℃) in the back section, thereby obtaining high-quality thin films.
Optimize material properties
Temperature gradient can induce changes in the internal stress distribution of materials and improve their mechanical properties. For example, in metal heat treatment, controlling the cooling rate through multiple temperature zones can refine the grain structure, improve material strength and toughness.
2. Support multi-step continuous process
Reduce the number of sample transfers
A single temperature zone furnace requires multiple furnace openings to transfer samples for different temperature treatments, while a multi temperature zone furnace can achieve the entire process of preheating, reaction, cooling, etc. in the same furnace. For example, in semiconductor device manufacturing, samples can be sequentially subjected to low-temperature oxidation layer removal, medium temperature doping, and high-temperature annealing isothermal zone to avoid intermediate contamination and oxidation.
Improve process efficiency
In continuous processing mode, the sample processing time is reduced by more than 50%, while reducing the number of device starts and stops and lowering energy consumption. For example, in catalyst preparation, a multi zone furnace can simultaneously complete precursor decomposition, active component loading, and carrier modification, reducing the single batch processing time from 8 hours to 3 hours.
3. Enhance experimental flexibility and reproducibility
Independently control parameters of each temperature zone
Each temperature zone can be individually set with parameters such as temperature, heating rate, and holding time, supporting comparative experimental design. For example, when studying alloy phase transformation, different cooling rate temperature zones can be set simultaneously to compare the differences in material microstructure.
Improve process stability
The multi zone furnace reduces temperature fluctuations inside the furnace (usually ≤± 1 ℃) by zone temperature control, ensuring experimental reproducibility. For example, in the synthesis of nanomaterials, temperature fluctuations can lead to a wider particle size distribution, while multi zone furnaces can stably control the reaction temperature and obtain monodisperse nanoparticles.
4. Adapt to diverse material processing needs
Compatible with different material systems
A multi zone furnace can simultaneously process materials that require different temperature conditions. For example, in the preparation of composite materials, the ceramic matrix needs to be sintered at 1200 ℃, while the metal reinforcement phase needs to be tempered at 800 ℃. Multi zone furnaces can achieve collaborative processing through zone temperature control.
Support the preparation of gradient materials
By controlling the temperature gradient, materials with gradient changes in composition or structure can be prepared. For example, in the preparation of functionally graded materials (FGM), a multi zone furnace can achieve a smooth transition from metal to ceramic, avoiding interface stress concentration.
5. Typical application scenarios
Semiconductor industry
Used for processes such as wafer annealing and oxide layer growth, controlling doping concentration and oxide layer thickness through multiple temperature zones.
In the field of new energy
In the preparation of electrode materials for lithium-ion batteries, multi zone furnaces can achieve continuous processing steps such as precursor mixing, pre firing, and high-temperature solid-state reactions.
Research on Nanomaterials
Used for the controllable synthesis of nanomaterials such as quantum dots and carbon nanotubes, adjusting reaction kinetics parameters through temperature gradients.
6. Technical implementation method
Multi zone tube furnaces typically adopt the following design:
Partition heating: Each temperature zone is equipped with independent heating elements (such as resistance wires, silicon carbide rods) and a temperature control system.
Thermal insulation structure: Multiple layers of insulation materials (such as alumina fibers) are used to reduce thermal interference in the temperature range.
Airflow control: By adjusting the atmosphere composition and flow rate of each temperature zone through independent gas paths, it supports various environments such as oxidation, reduction, and inertness.
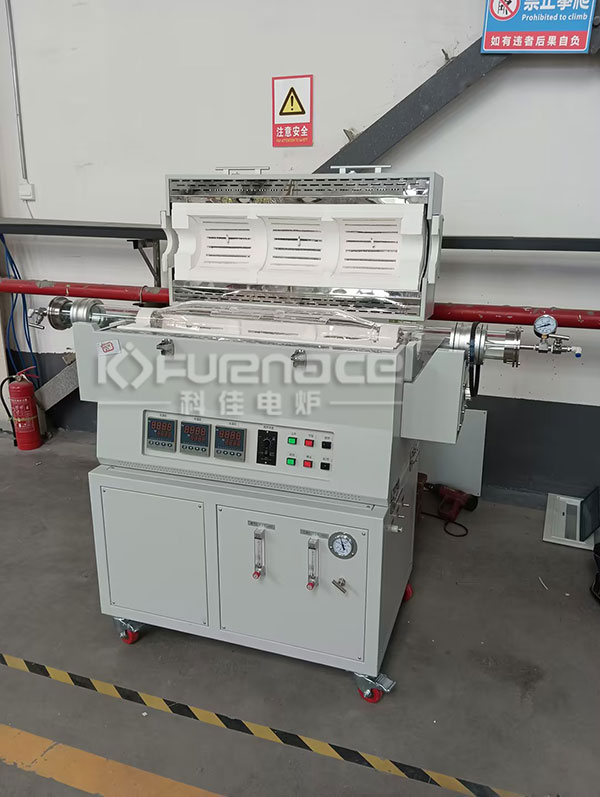
Customized Multi Gradient Rotating Tube Furnace (Click on the image to view product details)
In general, multi temperature zone tube furnaces are highly favored by university laboratories, industrial and mining enterprise laboratories, etc. due to their characteristics of individually controllable temperature zone, higher thermal efficiency, and more uniform temperature field. It is recommended to consult relevant technical personnel before choosing, so as to customize a more suitable multi temperature zone tube furnace for oneself!Click to learn more tube furnaces! Or click on online customer service to learn more about product information!