The temperature selection of box type resistance furnaces should comprehensively consider material characteristics, process requirements, equipment capabilities, and safety regulations. Reasonable setting of temperature parameters can ensure the quality and efficiency of experiments or production. Let’s take a detailed look at how to choose the temperature when choosing a box type resistance furnace!
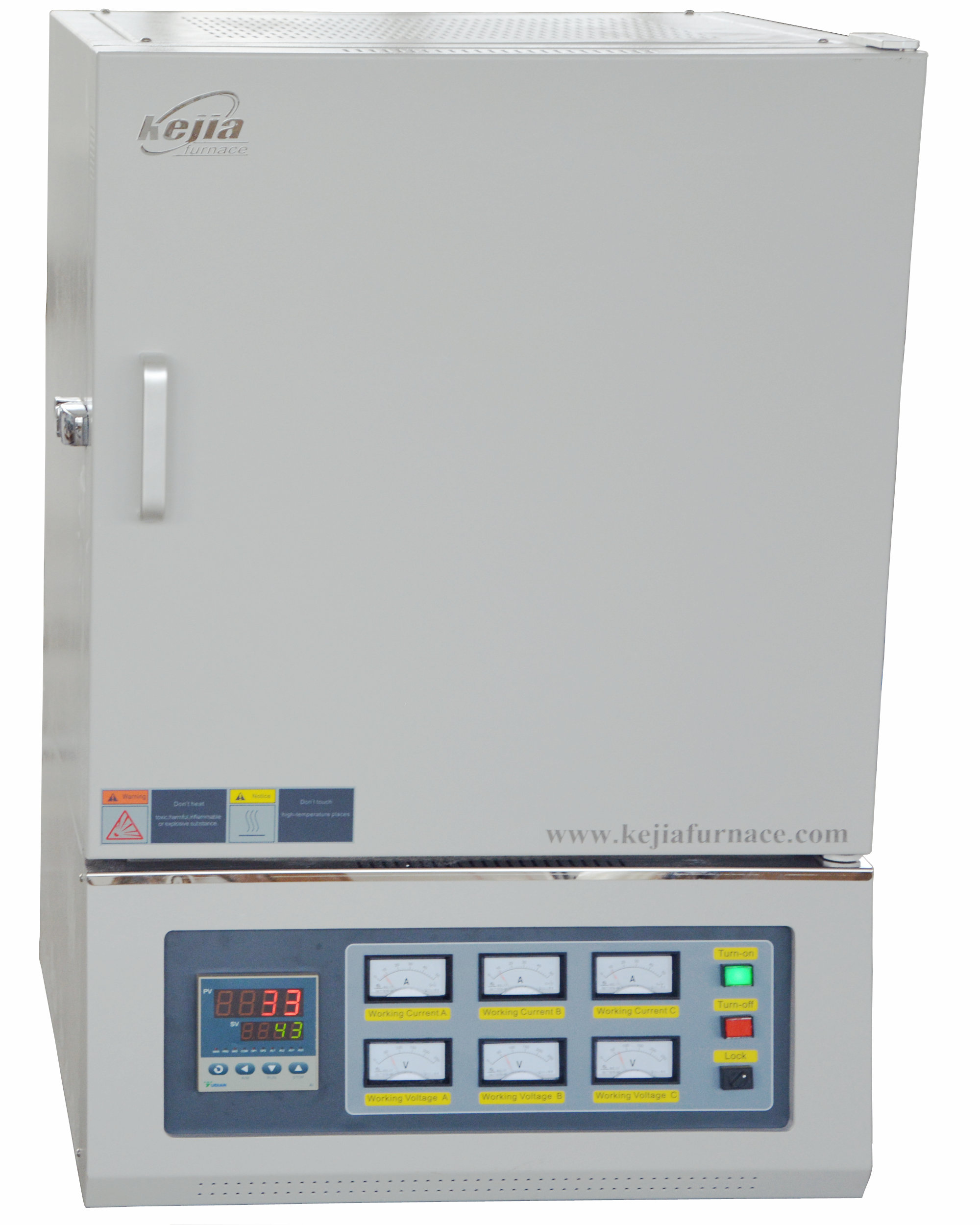
Box type resistance furnace with a maximum temperature of 1200 ℃ (click on the image to view product details)
1. Clarify process requirements: the core basis for temperature
Material heat treatment characteristics
Phase transition temperature: The austenitization temperature of metal materials (such as steel) (727-950 ℃) and the sintering temperature of ceramics (1200-1600 ℃) must strictly follow the material phase diagram.
Thermal decomposition temperature: Organic materials (such as polymers) should be below their decomposition temperature (such as PET decomposition temperature of about 350 ℃) to avoid structural damage.
Reaction activation temperature: Chemical synthesis (such as catalyst preparation) needs to reach the temperature corresponding to the reaction activation energy (such as 400-500 ℃ for ammonia synthesis).
Process objectives
Annealing/Tempering: Metal annealing is usually below Ac1 (such as carbon steel 550-650 ℃), and the tempering temperature is selected according to the hardness requirements (low-temperature tempering 150-250 ℃, high-temperature tempering 500-650 ℃).
Sintering/melting: Ceramic sintering needs to be close to the melting point of the material (such as alumina sintering temperature of 1550-1650 ℃), and glass melting needs to be 1200-1500 ℃.
2. Equipment Capability Matching: Temperature Range and Accuracy
Nominal Temperature Range
Confirm the maximum temperature of the furnace body (such as 1100 ℃, 1200 ℃, 1700 ℃, etc.), ensuring that the process temperature is within the rated range of the equipment (usually leaving a margin of 10-20 ℃).
Example: If sintering at 1200 ℃ is required, a furnace type with a rated temperature of ≥ 1250 ℃ should be selected.
Temperature uniformity
There is a gradient in the temperature field inside the box furnace (high in the center and low at the edges), and the uniformity needs to be evaluated based on the furnace size and heating element layout.
Optimization method:
Preheating stage: Slowly increase the temperature (e.g. 5 ℃/min) to reduce thermal stress.
Material placement: Avoid blocking the heating element and maintain a distance of ≥ 50 mm between the material and the furnace wall.
Mixing/flipping: For powder or granular materials, the furnace can be stopped and stirred in stages (safety precautions should be taken).
precision
Choose a PID intelligent temperature control system to ensure temperature fluctuations of ≤ ± 1 ℃ (precision experiment) or ± 5 ℃ (industrial production).
Regularly calibrate thermocouples (e.g. every 6 months) to avoid temperature deviation caused by sensor drift.
3. Safety and Operating Standards: Boundary Conditions for Temperature Selection
over temperature protection
Set an over temperature alarm threshold (usually 20-50 ℃ higher than the target temperature) and link to cut off the heating power supply.
Example: When the target temperature is 1000 ℃, the over temperature protection is set to 1050 ℃.
Heating rate control
To avoid material cracking or equipment damage caused by rapid heating:
Metal heat treatment: heating rate ≤ 10 ℃/min (thicker section workpieces need to be slower).
Ceramic sintering: Heating rate ≤ 5 ℃/min (slower during densification stage).
Chemical vapor deposition (CVD): The heating rate needs to be matched with the gas flow rate (such as 1-3 ℃/min).
Selection of cooling method
Natural cooling: suitable for processes that are insensitive to temperature gradients (such as air cooling after metal annealing).
Forced air cooling: Shorten cooling time (such as rapid cooling to room temperature for ceramic demolding).
Program controlled cooling: For quenching processes, precise control of cooling rate is required (such as rapid cooling of steel quenching from 850 ℃ to below 200 ℃).
4. Typical scenario temperature selection example
Metal heat treatment
Quenching: Carbon steel is heated to 820-860 ℃ (austenitized) and then rapidly quenched in water or oil after insulation.
Ceramic sintering
Aluminum oxide ceramic: Keep at 1550 ℃ for 2 hours, with a heating rate of 3 ℃/min, and cool naturally.
Silicon nitride ceramics: Keep at 1700 ℃ for 4 hours and protect against oxidation with nitrogen gas.
chemical synthesis
Hydrothermal synthesis: react at 200 ℃ for 12 hours, requiring the use of a high-pressure reaction vessel (box type furnace needs to be equipped with a pressure vessel).
Sol gel method: dry the gel at 60 ℃ and calcine it at 500 ℃ to remove organic matter.
5. Common Problems and Solutions
The temperature cannot reach the set value
Reason: Heating element aging, thermocouple disconnection, insufficient power.
Solution: Replace heating elements (such as silicon carbon rods, silicon molybdenum rods) and check the wiring of the temperature control system.
Excessive temperature fluctuations
Reason: PID parameters were not optimized, furnace door sealing was not tight, and material load was uneven.
Solution: Adjust PID parameters (such as increasing integration time), replace sealing strips, and evenly distribute materials.
local overheating
Reason: Unequal power distribution of heating elements and blockage caused by material accumulation.
Solution: Redesign the layout of heating elements (such as zone temperature control) and use alumina crucibles to disperse materials.
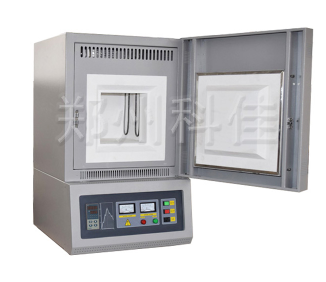
Box type resistance furnace with a maximum temperature of 1700 ℃ (click on the image to view product details)
Summarize
The temperature selection of box type resistance furnaces should be based on material characteristics and process objectives, combined with equipment capabilities (temperature range, uniformity, temperature control accuracy) and safety regulations (over temperature protection, heating rate) for comprehensive design. In practical operation, it is recommended to optimize the temperature curve through small-scale experiments (such as segmented insulation time) and record key parameters (such as actual temperature and heating rate) to guide subsequent production.Click to learn more box type resistance furnaces! Or click on online customer service to learn more about product information!