Common Faults and Treatment of Temperature Control of Box Type Resistance Furnace
Time:2020-09-11 14:17 Click:
The following are common failure phenomena, causes and measures to be taken for box-type resistance furnace temperature controllers.
Phenomenon 1: heating up too slowly or not reaching the maximum working temperature
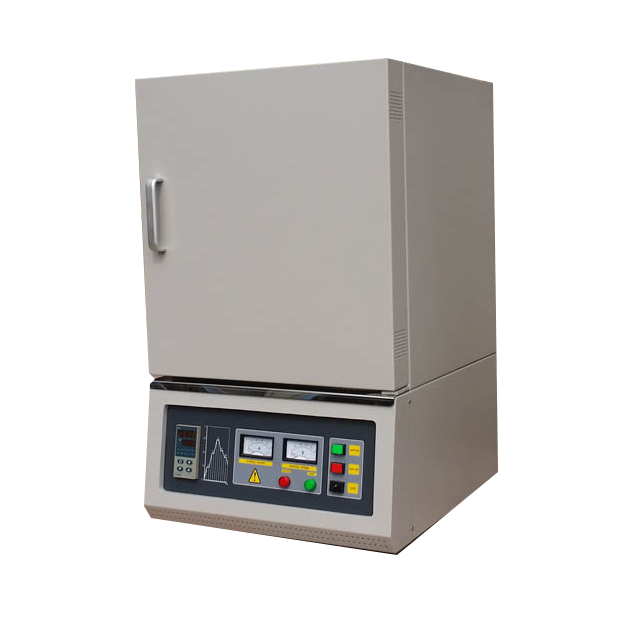
the reason:
1. The grid voltage is too low;
2. The unbalanced value of three-phase current exceeds 20%;
3. The electric heating element is open circuit or lack of phase;
4. The resistance value of the electric heating element does not meet the requirements;
5. The power of the electric heating element is reduced;
6. There is a short circuit phenomenon in the electric heating element;
7. Too much furnace charge;
8. The performance of heat shield or furnace lining deteriorates, and the heat dissipation is too large;
9. The connection method of the electric heating element is wrong;
10. Low output voltage of furnace transformer;
11. The output power of the power regulator is too small;
12. The temperature control device fails;
Measures:
1. Check the grid voltage;
2. Measure whether the resistance values of the three groups of heating elements are consistent;
3. Check the fault point of the electric heating element;
4. Measure whether the limits of the three groups of electric heating elements are within the allowable range;
5. Replace electric heating elements;
6. Eliminate short-circuit points;
7. Reduce the loading amount;
8. Replace the insulation layer, or reduce the heat dissipation, such as the cooling water flow is the most;
9. Correctly connect electric heating elements;
10. Check the furnace transformer;
11. Check or adjust the power regulator;
12. Troubleshoot the control device;
Phenomenon 2: Poor temperature uniformity
the reason:
1. Unreasonable power distribution;
2. The electric heating element is open;
3. The unreasonable furnace structure leads to excessive local heat dissipation;
4. Poor sealing of the furnace and excessive local heat dissipation;
5. The gas circulation of the furnace with fan is uneven or the wind is insufficient;
6. The thermocouple installation position or insertion depth cannot reflect the true temperature;
7. The distribution of electric heating elements is unreasonable;
8. The bottom temperature of the furnace is low;
9. The heating power supply lacks phase and the fuse is broken;
Measures:
1. Recalculate and improve the power configuration;
2. Replace the broken electric heating element;
3. Improve the furnace structure or improve the cooling method;
4. Check the furnace sealing and eliminate the bad sealing factors;
5. Place the workpiece reasonably to increase the wind power of the fan;
6. Reasonably choose the installation position or insertion depth of the thermocouple;
7. Adjust the distribution of electric heating elements;
8. Increase the heating power of the furnace bottom;
9. Check the heating power circuit;
Phenomenon 3: Poor sealing
the reason:
1. The furnace cover sealing ring is aging;
2. There is air leakage in the furnace body;
3. Poor sealing of vacuum pipelines and valves;
4. Poor sealing at the electrode;
5. Poor sealing of thermocouple insertion manhole;
6. The vacuum gauge is not well sealed at the inserting place;
7. The spare hole is poorly sealed;
Measures:
1. Replace the furnace cover sealing ring;
2. Check the furnace body and eliminate leaks;
3. Check the sealing condition of the vacuum system;
4. Gongxin cleans and installs electrodes;
5. Reinstall the thermocouple;
6. Check and reinstall the vacuum gauge;
7. Check the seal of the spare hole;
Please leave a message here. We will reply you in 24 hours.