When customizing a muffle furnace, the following core parameters can be personalized according to specific application scenarios, material characteristics, and process requirements to meet diverse needs such as high-temperature heat treatment, material synthesis, and experimental research. Let’s take a detailed look below!
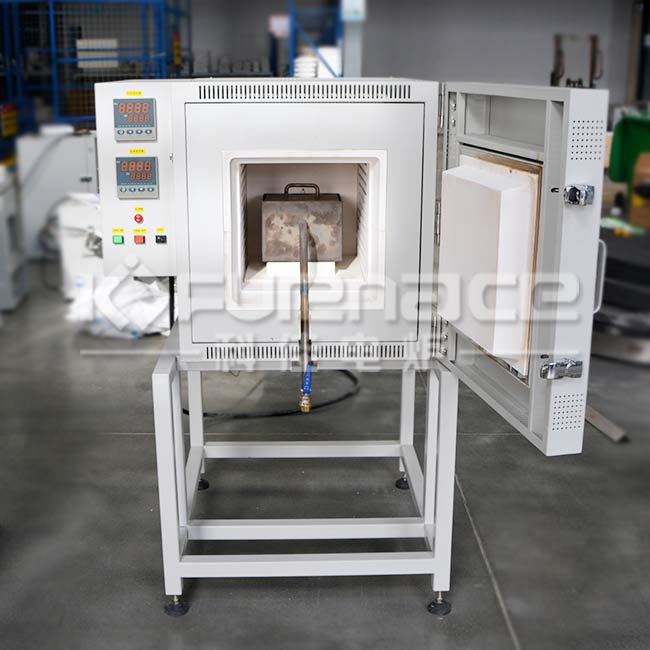
Customized pyrolysis carbonization furnace (click on the image to view product details)
1. Temperature parameters
maximum service temperature
Range: Typically between 200 ℃ and 1800 ℃, can be customized according to material characteristics (such as ceramic sintering requiring over 1600 ℃, metal annealing may only require 1000 ℃).
Customization significance: To avoid process failure caused by insufficient temperature or equipment cost and energy consumption caused by excessive temperature.
Temperature uniformity
Range: ± 1 ℃~± 10 ℃ (temperature difference at various points inside the furnace).
Customization method: Improve uniformity by optimizing the layout of heating elements (such as 3D heating), increasing the number of thermocouples, and using ceramic fiber furnaces.
Application scenarios: Temperature sensitive processes such as precision ceramic sintering and semiconductor material oxidation.
heating rate
Range: 1 ℃/min~20 ℃/min (conventional models are 5-20 ℃/min).
Customization requirement: Rapid heating can shorten the process cycle (such as metal quenching), but it is necessary to balance the service life of heating elements and furnace thermal stress.
cooling rate
Method: Natural cooling, air cooling, water cooling, or oil cooling.
Customization significance: controlling the phase transition process of materials (such as slow cooling required for glass annealing), or improving production efficiency (such as rapid cooling of metal components).
2. Furnace structure and dimensions
furnace volume
Scope: From laboratory small furnaces (1L~10L) to industrial large furnaces (1m ³ or more).
Customization factors: Design based on sample size, batch production requirements, or experimental space limitations.
Furnace shape
Types: Box type (universal), tube type (suitable for long strip samples), well type (vertical loading, suitable for shaft parts), lifting type (convenient for loading and unloading heavy objects).
Application scenarios: Tube furnaces are used for the preparation of nanomaterials, while well furnaces are used for gear quenching.
Furnace material
Refractory bricks: Low cost, but average insulation performance (suitable for low temperature or low-cost needs).
Ceramic fiber: lightweight, excellent insulation performance (energy-saving by more than 30%), but slightly lower temperature resistance than alumina.
Aluminum oxide/silicon carbide: resistant to high temperatures (≥ 1600 ℃), suitable for high-temperature sintering or corrosive atmospheres.
Customization significance: Balancing cost, temperature resistance, and insulation performance.
3. Heating element and power
Heating element type
Resistance wire: Low cost, suitable for low temperatures (≤ 1200 ℃).
Silicon carbon rod: resistant to high temperatures (≤ 1400 ℃), heats up quickly, but is prone to oxidation.
Silicon molybdenum rod: high temperature resistance (≤ 1800 ℃), strong oxidation resistance, suitable for oxidizing atmospheres.
Graphite heating element: used in vacuum or inert atmosphere, with extremely high temperature resistance (≤ 2200 ℃), but requires oxidation prevention.
Power
Calculation method: determined based on furnace volume, target heating rate, and material heat capacity.
Customization significance: Insufficient power leads to slow heating, while excessive power increases energy consumption and equipment costs.
Distribution of heating zone
Type: Single zone, dual zone, or multi zone independent temperature control.
Application scenario: Multi zone temperature control can achieve temperature gradient (such as crystal growth) or compensate for heat loss at the edge of the furnace.
4. Atmosphere control
Atmosphere type
Options: Air (natural convection), Inert gas (N ₂ Ar)、 Reductive gases (H ₂ CO)、 Oxidative gas (O ₂).
Customization requirements: Metal annealing requires an inert atmosphere to prevent oxidation, while ceramic sintering may require an oxidizing atmosphere to promote grain growth.
Atmosphere flow and pressure
Range: Flow rate of 0.1~100L/min, pressure can be adjusted to micro positive pressure (leak proof) or negative pressure (vacuum compatible).
Customization significance: Accurately controlling the atmosphere can avoid material oxidation, decarburization, or the introduction of impurities.
Atmosphere circulation system
Options: No circulation (natural diffusion), mechanical stirring (to improve uniformity), gas displacement (to quickly switch atmospheres).
Application scenario: Gas stirring is suitable for large furnaces to ensure uniform distribution of atmosphere.
5. Control system
Temperature control method
Options: PID intelligent control, programmable temperature control meter, computer remote control.
Customization requirements: Complex processes (such as multi-stage heating, insulation, and cooling) require programmable control and support for data recording and export.
Safety protection
Function: Over temperature alarm, couple breaking protection, leakage protection, gas leakage detection, door lock interlock (to prevent accidental opening).
Customization significance: Ensure the safety of equipment and personnel, and comply with industrial safety standards.
human-computer interaction
Options: Touch screen, physical buttons, remote monitoring through mobile app.
Application scenario: Touchscreen is easy to operate, and remote monitoring is suitable for unmanned production.
6. Other customization options
Vacuum function
Type: Mechanical pump vacuum (≤ 10 ⁻² Pa) or molecular pump vacuum (≤ 10 ⁻⁵ Pa).
Application scenario: Vacuum sintering can avoid material oxidation or achieve degassing treatment.
Observation window and lighting
Option: High temperature resistant quartz window, LED lighting for real-time observation of sample status.
Automated integration
Function: Linkage with robotic arms and conveyor belts to achieve fully automatic loading and unloading and process control.
Application scenario: Integration of large-scale production lines to improve production efficiency.
Special materials and coatings
Options: Spraying alumina coating on the inner wall of the furnace (anti adhesion), surface treatment of heating elements (prolonging service life).
Customized Process Suggestions
Clear requirements: Determine key parameters such as material type, process temperature, atmosphere requirements, sample size, etc.
Consulting vendors: Provide a list of requirements, obtain technical solutions and quotations.
Sample testing: Verify key parameters (such as temperature uniformity) to ensure compliance with process requirements.
Sign the contract: specify the delivery date, after-sales service, and warranty terms.
Typical application cases
High temperature ceramic sintering: customized 1700 ℃ silicon molybdenum rod heating, alumina fiber furnace, inert atmosphere protected box furnace.
Metal heat treatment: customized well furnace with 1200 ℃ silicon carbon rod heating, hydrogen reduction atmosphere, and rapid cooling.
Semiconductor oxidation: Customized 1100 ℃ resistance wire heating, oxygen atmosphere, multi-stage temperature control tube furnace.
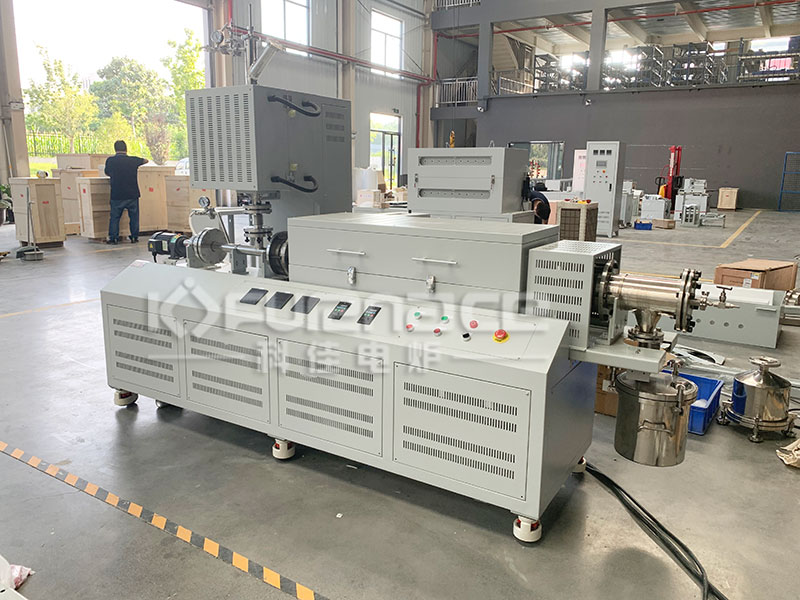
Customized multi zone rotary tube furnace with preheating (click on the image to view product details)
By customizing parameters, the muffle furnace can better match user process requirements, improve product quality and production efficiency, while reducing long-term operating costs. You can communicate the parameters with relevant technical personnel before customization, so as to customize a muffle furnace that is more suitable for your own experimental or production needs!Click to learn more Customized muffle furnaces! Or click on online customer service to learn more about product information!