When choosing a calcination tube furnace in the laboratory, it is necessary to comprehensively consider core dimensions such as temperature range, sample adaptability, temperature zone design, functional configuration, and safety. Let’s analyze them in detail below!
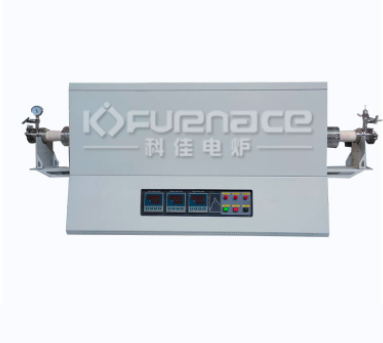
A commonly used experimental multi temperature zone tube furnace (click on the image to view product details)
1. Temperature range: Match experimental requirements
Maximum temperature and continuous operating temperature
Select the maximum temperature limit for the tube furnace based on the melting point or reaction temperature of the experimental materials (such as metals, ceramics, and composite materials). For example, metal melting requires over 1600 ℃, while ceramic sintering may only require 1200 ℃.
Pay attention to the continuous operating temperature (i.e. the temperature at which the equipment can operate stably for a long time) to avoid damage to the heating element caused by overheating. For example, MoSi ₂ heating elements (1600-1800 ℃) are prohibited from working for long periods of time below 800 ℃, otherwise they are prone to powdering and failure.
Heating element type
Resistance wire: 250-1250 ℃, suitable for low-temperature experiments (such as material drying).
Silicon carbide: 1300-1600 ℃, with high cost-effectiveness in the medium temperature range.
MoSi ₂ (molybdenum silicon rod): 1600-1800 ℃, commonly used as a heating rod in high-temperature experiments, but attention should be paid to the lower limit of the temperature used.
Graphite: capable of reaching temperatures above 2300 ℃, suitable for ultra-high temperature experiments (such as carbon material processing), but requires inert gas or high vacuum protection to prevent oxidation.
2. Sample adaptability: compatibility of size and material
Crucible selection
Quartz crucible: ≤ 1200 ℃, suitable for oxidizing atmospheres such as air and oxygen.
Aluminum oxide crucible: ≤ 1800 ℃, high temperature resistance and good chemical stability, but avoid using mullite crucible when the heat treatment temperature exceeds 900 ℃.
Graphite crucible: ≤ 2300 ℃, suitable for reducing atmosphere (such as hydrogen, vacuum), but oxidation should be prevented.
Furnace tube diameter and length
Select the pipe diameter based on the sample volume to ensure that there is still space for hot gas circulation (temperature difference ≤± 1 ℃) after loading the crucible. For example, when processing powder samples, quartz tubes (≤ 1200 ℃) or corundum tubes (≤ 1700 ℃) are common choices.
The length of the furnace tube needs to match the experimental batch requirements. The multi temperature zone tube furnace can extend the constant temperature zone and is suitable for processing multiple samples simultaneously.
3. Temperature Zone Design: Temperature Uniformity Control
Single temperature zone vs multi temperature zone
Single temperature zone: The structure is simple and the cost is low, but the constant temperature zone is relatively short (usually ≤ 300mm), suitable for small samples or single temperature experiments.
Multi temperature zone: Segmented temperature control is achieved through multiple thermocouples, with a longer constant temperature zone (such as up to 900mm in 3 temperature zones), suitable for experiments that require gradient temperature (such as material phase transition research).
Accuracy of constant temperature zone
The temperature difference in the constant temperature zone should be ≤ ± 1 ℃ to ensure uniform heating of the sample. For example, the growth of graphene requires precise control of the temperature field to avoid structural defects caused by local overheating.
4. Function configuration: meet special experimental requirements
atmosphere control
Vacuum function: Suitable for heat treatment of oxidation sensitive materials (such as titanium alloys) to prevent the formation of an oxide layer.
Inert gas protection: such as nitrogen and argon, used for reducing reactions (such as metal sulfide oxidation) or preventing material volatilization.
Special gas treatment: Hydrogen reduction and corrosive gases (such as Cl ₂) require dedicated tube furnaces with leak proof design.
Rapid Heat Treatment (RTP)
The heating rate can reach over 50 ℃/s, suitable for experiments such as rapid annealing and thin film preparation (such as semiconductor device manufacturing).
Rotating furnace tube
By rotating, the powder sample is uniformly heated, which is suitable for coating processes (such as nuclear fuel particle cladding) or preventing agglomeration.
5. Security: Operation and equipment protection
Overtemperature alarm and automatic power-off
When the temperature exceeds the set value, the equipment should automatically cut off the power and sound an alarm to prevent damage to the heating element or scrap of the sample.
Leakage protection and emergency shutdown
Equipped with leakage protection devices to avoid the risk of electric shock; The emergency stop button can quickly terminate the experiment and respond to unexpected situations.
Air tightness design
Vacuum tube furnaces require metal sealing (such as nickel chromium alloy flanges) to ensure a vacuum degree of ≤ 10 ⁻ Pa and prevent gas leakage.
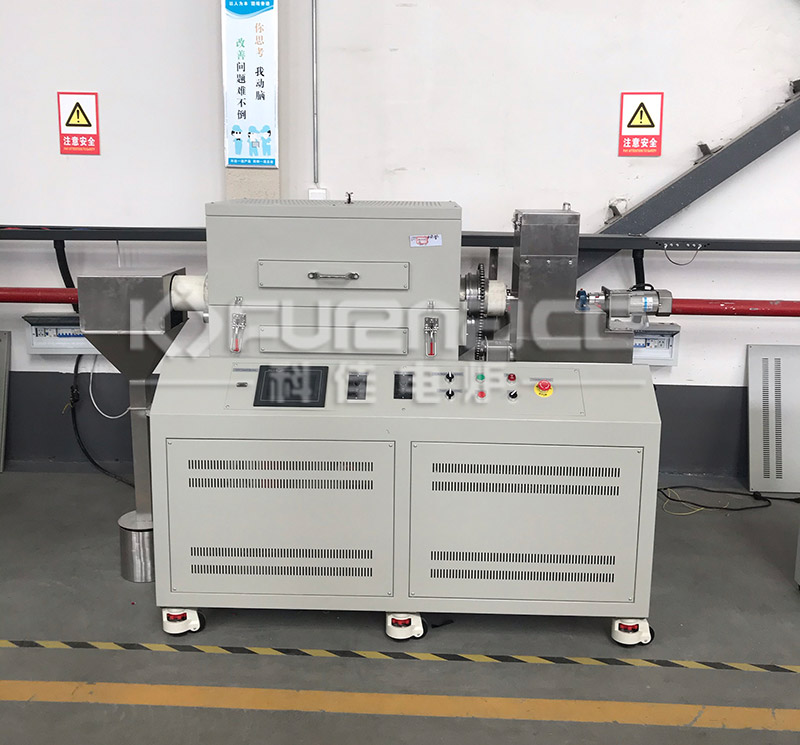
Commonly used continuous feeding and discharging sintering furnace (click on the picture to view product details)
In general, when choosing a tube furnace for laboratory calcination, attention should be paid to the above issues. Before choosing, it is necessary to communicate with relevant technical personnel about the experimental parameters you need, so as to customize a calcination tube furnace that is more suitable for your experiment!Click to learn more tube furnaces! Or click on online customer service to learn more about product information!