The customized service of multi temperature zone rotary tube furnace has significant advantages in scientific research and industrial fields, which can accurately match diverse needs, improve experimental efficiency and product quality. Let’s take a detailed look at the advantages and characteristics of customized multi temperature zone rotary tube furnaces below!
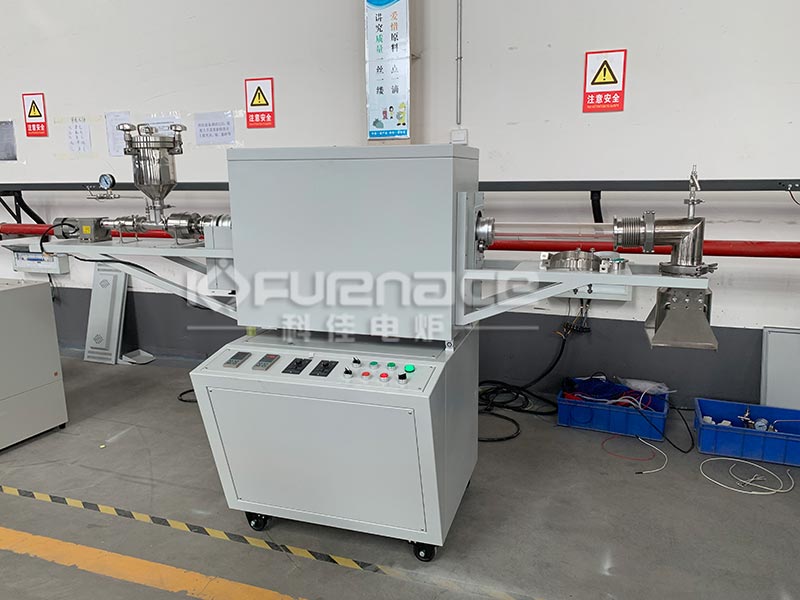
Experimental Two Gradient Rotating Tilt Tube Furnace (Click on the image to view product details)
1.Accurately match experimental requirements and break through the limitations of standard equipment
Temperature gradient control
Multi zone independent temperature control: 2-5 independent temperature zones can be customized, and the temperature range (such as room temperature to 1700 ℃) and heating rate of each zone can be set separately to achieve precise temperature gradient distribution.
Application scenario: In graphene synthesis, the carbon source is cracked in the first high-temperature zone (1000 ℃), and the ordered growth is promoted in the second low-temperature zone (600 ℃) to avoid disorderly stacking.
Improved temperature control accuracy: Customize PID algorithm or fuzzy control technology to control temperature fluctuations within ± 1 ℃, meeting the temperature sensitive experimental needs of semiconductor materials, catalysts, etc.
Optimization of rotation and tilt functions
Adjustable rotation speed: Supports 0-15rpm stepless speed regulation to ensure uniform heating of powder, liquid, or film samples.
Case: A certain university customized a rotary tube furnace to process ceramic powder at a speed of 5rpm, which increased the density of the sintered body by 12% and reduced the porosity to below 3%.
Tilt angle customization: adjustable design from 0 ° to 90 °, suitable for special processes such as gas exchange and liquid dripping.
Application: In chemical vapor deposition (CVD), a 30 ° tilt angle is used to promote gas flow on the sample surface, improving the uniformity of the deposition layer to over 95%.
2.Flexibly adapt to sample characteristics and expand application boundaries
Customization of furnace tube size and material
Diameter and length expansion: Customize furnace tubes according to sample size (such as Φ 200mm × 1500mm), supporting large workpieces or batch processing.
Industrial case: A certain enterprise customized a large-diameter tube furnace that can process 50kg of metal powder in a single operation, increasing production efficiency by three times.
Material selection: Quartz tube (transparent observation, corrosion-resistant), stainless steel tube (high temperature strength), or corundum tube (resistant to rapid cooling and heating) can be configured as needed.
Research application: In experiments with strong corrosive atmospheres (such as Cl ₂), using Hastelloy furnace tubes can extend the service life to more than 5 years.
Upgrade of atmosphere control system
Multi gas injection and mixing: Supports independent control of 3-5 gas channels, with precise proportional adjustment through a mass flow meter (MFC) (e.g. H ₂: Ar=1:9).
Energy field: In the preparation of fuel cell catalysts, customized H ₂/Ar mixed atmosphere is used to narrow the particle size distribution of Pt nanoparticles (D50=2.5nm ± 0.3nm).
Vacuum degree improvement: equipped with a dual stage vacuum pumping system of mechanical pump and molecular pump, with a maximum vacuum degree of ≤ 10 ⁻⁴ Pa, to meet the requirements of high-purity material synthesis.
Semiconductor case: In SiC epitaxial growth, vacuum environment can reduce impurity doping and lower defect density to below 10 ⁵ cm ⁻ ².
3.Improve experimental efficiency and safety, and reduce overall costs
Rapid heating and cooling
Customization of heating power: Choose a heating power of 10-50kW according to the furnace volume to shorten the heating time (such as only 30 minutes from room temperature to 1200 ℃).
Water cooling jacket design: By circulating cooling water to accelerate cooling, the experimental cycle is shortened by 40%, making it suitable for continuous production scenarios.
Industrial data: A certain photovoltaic enterprise customized a water-cooled tube furnace, and the daily production capacity of a single line increased from 200kg to 350kg.
Enhanced security protection
Multiple alarm system: automatic alarm and power cut-off for faults such as overheating, gas interruption, and leakage, to avoid equipment damage or personnel injury.
Explosion proof structural design: The furnace body adopts explosion-proof doors and pressure relief valves to ensure safety in flammable atmosphere experiments such as hydrogen gas.
Research support: A university laboratory successfully avoided three potential explosion accidents by customizing an explosion-proof tube furnace.
Modularity and Scalability
Reserved interface design: Supports future upgrades to automation control systems and online monitoring modules (such as infrared temperature measurement and gas analyzers).
Expansion capability of temperature zone: Initially customized equipment with 2 temperature zones, it can be expanded to 4 temperature zones through the installation of heating modules in the later stage to protect investment.
Long term plan: A research institute will customize tube furnaces in stages, gradually increasing experimental capabilities according to demand within 5 years, and reducing total costs by 25%.
4. Customized cases and data support
Materials synthesis field
Case: A material laboratory customized a three temperature zone rotary tube furnace for synthesizing two-dimensional transition metal sulfides (2D TMDs).
Effect: By using sulfurized metal precursor in the high temperature zone (800 ℃) in the front section, controlling the number of layers in the medium temperature zone (500 ℃) in the middle section, and annealing in the low temperature zone (300 ℃) in the back section, the yield of single-layer MoS ₂ was increased from 15% to 68%.
Energy storage field
Case: A battery company customized a vacuum atmosphere rotary tube furnace for the preparation of negative electrode materials (Si/C composite) for lithium-ion batteries.
Effect: Through rotational heat treatment in Ar atmosphere, Si particles were uniformly dispersed in the carbon matrix, and the initial charge discharge efficiency increased from 72% to 89%. After 100 cycles, the capacity retention rate reached 91%.
Semiconductor manufacturing field
Case: A chip manufacturer customized a high vacuum multi temperature zone tube furnace for GaN epitaxial growth.
Effect: By precisely controlling the ratio of NH3/N ₂ atmosphere and temperature gradient, the dislocation density of epitaxial layers is reduced to 5 × 10 ⁶ cm ⁻ ², and the luminous efficiency of LED devices is improved by 30%.
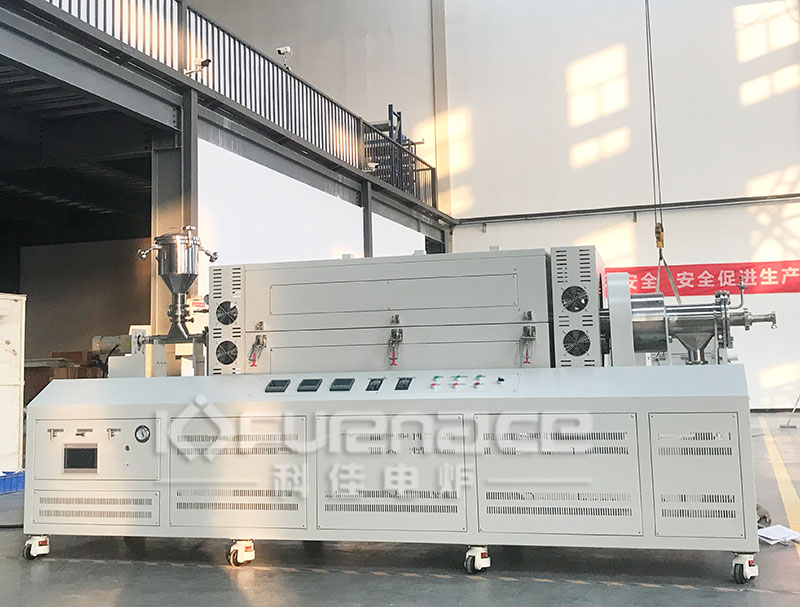
KJ-TX1000-L150CK3W Three Gradient Tilted Rotating Tube Furnace (Click on the picture to view product details)
Overall, customizing a multi temperature zone rotary tube furnace has many advantages. It is possible to communicate the parameters with relevant technical personnel before customization, so as to customize a multi temperature zone rotary tube furnace that is more suitable for one’s experimental or production needs!Click to learn more tube furnaces! Or click on online customer service to learn more about product information!